Container Homes: The Future of Modular Construction
Modular construction, especially container homes, represents a significant shift in how buildings are designed and assembled. This method involves creating sections of a structure in a factory setting before transporting them to the construction site for final assembly. The use of shipping containers as building blocks has gained traction due to their strength, availability, and cost-effectiveness. These containers are typically made from corten steel, which is highly resistant to corrosion, making them durable for long-term use.
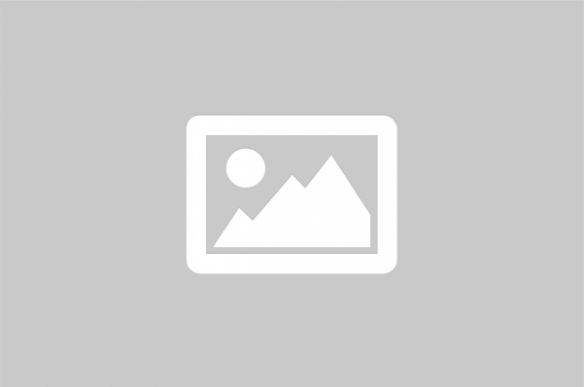
Benefits of Container Homes
Container homes offer numerous advantages, making them an attractive option for homeowners and developers alike. One of the most notable benefits is affordability. The cost of a basic container home can be significantly lower than that of a conventional house, with prices ranging from $10,000 to $50,000 depending on size and customization. Additionally, the streamlined construction process reduces labor costs and minimizes delays caused by weather or other on-site issues.
Another key advantage is sustainability. Repurposing shipping containers reduces the demand for new construction materials and helps decrease the carbon footprint associated with building projects. Many container homes also incorporate energy-efficient features such as solar panels, rainwater harvesting systems, and high-quality insulation, further enhancing their eco-friendly appeal. The modular design also allows for easy scalability, enabling homeowners to add more units as their needs evolve.
Challenges and Considerations
While container homes offer many benefits, they are not without challenges. One common concern is insulation. Shipping containers are made of metal, which conducts heat and cold, making temperature regulation a potential issue. Proper insulation is essential to ensure comfort and energy efficiency. Additionally, local building codes and zoning laws may restrict the use of container homes in certain areas, so it is crucial to research regulations before starting a project.
Another consideration is the need for structural modifications. Cutting openings for doors and windows can weaken the container’s integrity if not done correctly. Reinforcements may be required to maintain structural stability. Furthermore, the limited width of shipping containers (typically 8 feet) can pose design challenges, requiring creative solutions to maximize space and functionality.
Comparison of Modular Construction Methods
Feature | Container Homes | Prefabricated Panel Homes | Traditional Construction |
---|---|---|---|
Cost | $10,000 – $50,000 | $50,000 – $150,000 | $150,000+ |
Construction Time | 2-4 months | 3-6 months | 6-12 months |
Customization | High | Moderate | High |
Sustainability | High (recycled materials) | Moderate | Low |
Future of Modular Construction
The future of modular construction, particularly container homes, looks promising as technology and design innovations continue to evolve. Advances in 3D printing and smart home integration are expected to further enhance the efficiency and functionality of modular buildings. Governments and organizations are also recognizing the potential of modular construction to address housing shortages and promote sustainable development. As awareness grows, container homes are likely to become a mainstream housing option, offering a blend of affordability, sustainability, and modern design.