Estimate Concrete Cost: Understanding and Calculating Cement Expenses
Concrete is the backbone of modern construction, playing a pivotal role in everything from skyscrapers to sidewalks. Understanding the costs associated with concrete, particularly cement, is crucial for anyone involved in construction projects, whether they are large-scale developers or DIY enthusiasts. Cement, as a primary component of concrete, significantly influences the overall cost of a construction project. Calculating cement expenses accurately can help in budgeting and financial planning, ensuring that projects are completed within the allocated resources.
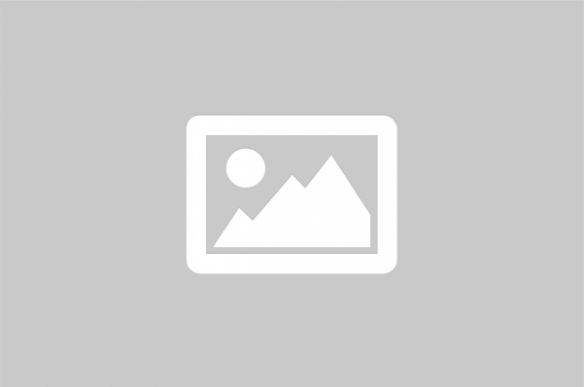
Estimating the cost of concrete is a fundamental step in planning any construction project. It involves understanding various factors that contribute to the overall expenses, with cement being a significant component. The cost of cement can vary based on several factors, including the type of cement used, the quantity required, and the location of the project. Additionally, market fluctuations and supplier pricing can also impact cement costs. Therefore, a thorough understanding of these elements is essential for accurate cost estimation.
Factors Affecting Cement Expenses
Several factors influence the cost of cement, and understanding these can help in making accurate estimations:
- Type of Cement: Different types of cement, such as Portland cement, white cement, and rapid-hardening cement, have varying costs. The choice of cement depends on the specific requirements of the project.
- Quantity: The amount of cement needed is directly proportional to the size and scope of the project. Larger projects will require more cement, thus increasing the cost.
- Location: The geographical location of the project can affect transportation costs and availability of cement, influencing the overall expense.
- Market Conditions: Fluctuations in the market, such as changes in demand and supply, can lead to variations in cement prices.
- Supplier Pricing: Different suppliers may offer varying prices for cement, so it is essential to compare options to find the most cost-effective solution.
Methods to Calculate Cement Expenses
Calculating cement expenses involves a few key steps that can help in achieving an accurate estimate:
- Determine the Volume of Concrete: Calculate the total volume of concrete required for the project. This can be done by multiplying the length, width, and height of the area to be concreted.
- Calculate Cement Requirement: Based on the mix design, determine the amount of cement needed per cubic yard or meter of concrete. This information is typically available in construction guidelines or can be provided by a structural engineer.
- Estimate Cement Cost: Multiply the amount of cement required by the current price per unit (e.g., per bag or ton) to get the total cement cost.
- Include Additional Costs: Consider any additional expenses such as transportation, taxes, and labor costs associated with handling and mixing the cement.
Comparison of Cement Types and Costs
Cement Type | Average Cost per Ton (USD) | Best Use Cases |
---|---|---|
Portland Cement | 100 – 120 | General construction, foundations, pavements |
White Cement | 200 – 250 | Decorative works, aesthetic finishes |
Rapid-Hardening Cement | 150 – 180 | Projects requiring quick setting, repairs |
Blended Cement | 90 – 110 | Eco-friendly projects, large-scale constructions |
Practical Tips for Optimizing Cement Costs
To ensure cost-efficiency in cement expenses, consider the following tips:
- Bulk Purchasing: Buying cement in bulk can often lead to discounts and lower per-unit costs.
- Supplier Comparison: Always compare prices from different suppliers to find the best deal.
- Efficient Mix Design: Use an optimized mix design to reduce the amount of cement needed without compromising on quality.
- Waste Reduction: Implement strategies to minimize waste during mixing and application to avoid unnecessary expenses.
Accurately estimating concrete costs, particularly cement expenses, is crucial for the successful execution of construction projects. By understanding the factors that influence cement costs, employing effective calculation methods, and implementing cost-saving strategies, project managers and builders can ensure that their projects remain within budget. With careful planning and informed decision-making, it is possible to achieve both financial efficiency and high-quality construction outcomes.
For more information on construction materials and cost estimation, visit Concrete Network and Portland Cement Association .